Thermographic inspection
Thermographic inspection is a nondestructive testing method, part of the maintenance schedule that is applied in different sectors. The power sector is one of them, and its use is quite widespread. It is applied to all types of facilities and voltage levels. Although, thermographic inspection points are located that reach an abnormal temperature, known as hot spots. These points are normally identified in both the equipment and facilities.
Table of Contents
The connections between the electrical elements are the places where they usually appear. They are mainly caused by a loose connection or by an incorrect tightening torque at the time of previous maintenance or assembly. This abnormality can surely cause a deterioration of the element as well as the connector and cause a breakdown. The connections between them are made through various electrical connectors.
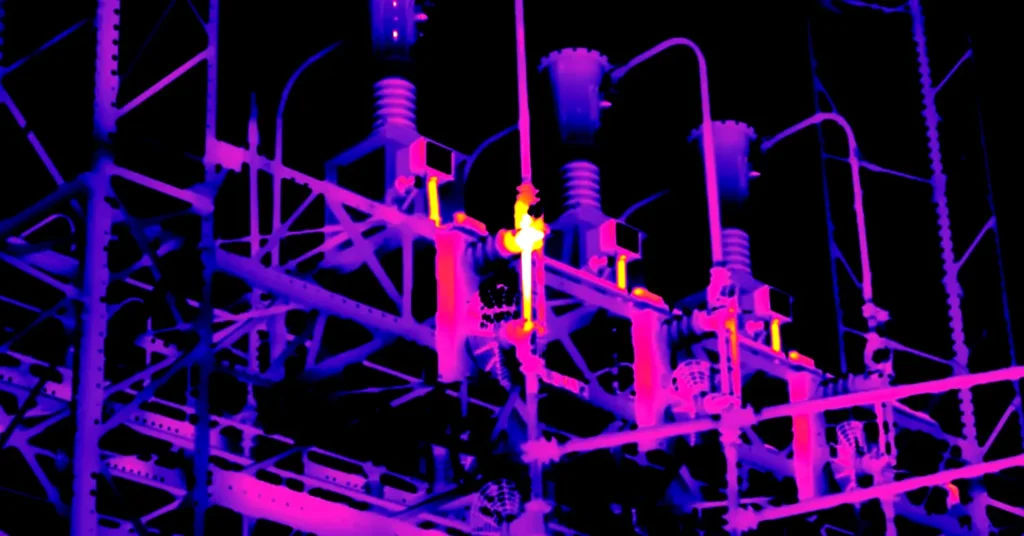
Thermographic inspection has advantages such as the ability to perform the inspection with the substation energized, at a low cost with very fast execution and effectiveness of the results. For all the above reasons, it is a highly appreciated part of preventive maintenance checks. However, it must be kept in mind that the importance of thermographic inspection is the identification of hot spots, but the accuracy of the value is in second place in importance. This is because, as the work is carried out in the switchyard, levels of precision similar to those of laboratory tests cannot be achieved.
Factors Influencing Thermographic Inspection
To carry out thermographic inspection correctly, a few factors that influence the accuracy of the measurements obtained must be considered. These factors can be of various types such as procedural factors, technical factors, and environmental related factors.
The procedural factors are those which are a consequence of the thermographic inspection. It must be performed by a qualified operator who has sufficient experience in the field.
Among the most important technical factors are the emissivity of the inspected elements of a circuit, the current that circulates through the circuit, the distance to the target element, and the specifications of the camera that is being used.
Regarding environmental factors, the most influential are ambient temperature, rain, wind, and solar radiation.
Conditions for Conducting Thermographic Inspections
Substations are generally high-voltage electrical facilities. Thermographic inspections are performed with the substation energized. The distances between various equipment are smaller than in other facilities. Therefore, a list of requirements must be met to carry out the work.
The personnel who will work must be qualified, and with adverse environmental conditions, the work cannot be carried out in wind, fog, rain, hail, or storm.
The operator who performs the thermographic inspection basically has a plan for the substation to be inspected during the day. Depending on the time of day, the week of the year, and even the day of the week, the load on the circuit and other circuit conditions will vary at every substation. Therefore, the most favorable condition for the detection of hot spots is when the nominal current circulates through the element.
This current is the maximum that can circulate through that circuit and corresponds to the substation working at full load. However, it cannot always happen. Therefore, a circuit can be inspected whenever it carries the full load. It is not usually recommended to go with the procedure in lightly charged circuits.
For detecting hot spots, a minimum current circulating through the element is necessary. A minimum load of 20% of the rated current must be set initially. Preset having been crossed by the current, the element acquires the service temperature. At some point, after the current begins to circulate, the service temperature acquired is thus stabilized. For this, at least 15 minutes must pass from powering on.
Subsequently, the change in the current that passes through the circuit does not have as much influence as the one produced since it is de-energized. This is because, in a substation, the current variations are usually minimal. Another requirement that must be met is that the tightening torque of the element connections must be as recommended by the manufacturer. Poor tightening will cause incorrect detection of the hot spot.
Regarding the load, when the thermographic inspection is carried out, the nominal current does not circulate. However, the same can be reached at any time. In addition, it must be considered that the higher the current through the element, the higher will be the element’s temperature. Therefore, the results thus obtained with a given current must be extrapolated to the case in which the nominal current circulates.
Considerable Action in a Hot Spot
The purpose of this inspection is to keep the equipment in operating condition, avoid possible failures, and maintain safety conditions for people and facilities. In this way, the service life of the equipment is increased. The measurements obtained will allow one to decide what actions to be taken. Basically, it can be reduced to three: the equipment parameters are adequate, and therefore there is no action to take; there is some variation in the parameters that indicates that more continuous monitoring of the equipment is necessary; or the results of the parameters that lead to performing an intervention on the equipment to return it to its normal service condition.
The goal of thermographic inspection is not to acquire knowledge of the temperature of an identified hot spot. The main goal is to discern whether to take any action on it. The table below shows the actions suggested by the American National Standards Institute. It is based on the difference in temperature between the hot spot and a reference.
The reference can be the ambient air’s temperature or that of another point or points with similar characteristics, such as that corresponding to another electrical phase. In each case, the ∆T ranges are different, being lower when the difference is between the hot spot and another element. The recommendations vary between a possible defect to observe, a follow-up of the hot spot through thermographic inspections with different time frequencies, or immediate repair to avoid a major defect.
Table from American National Standards Institute
Temperature Difference (∆T) Based on Comparisons between Similar Components under Similar Loading | Temperature Difference (∆T) Based on Comparisons between Component and Ambient Air Temperatures | Recommended Action on the Component |
1–3 °C | 1–10 °C | Possible deficiency; warrants investigation |
4–15 °C | 11–20 °C | Indicates probable deficiency; repair as time permits |
– | 21–40 °C | Monitor until corrective measures can be achieved |
>15 °C | >40 °C | Major discrepancy; repair immediately |
This article is a part of the Testing and commissioning page, where other articles related to topic are discussed in details.