DIFFERENT TYPES OF HTLS CONDUCTORS
High temperature low sag, htls conductors are modern conductors with enhanced thermal sag properties. Their maximum continous operating temperature is also increased, which aids in the conductor’s high current carrying capacity and also optimizing transmission network of a region.
Table of Contents
These high performance conductors are also used for uprating existing transmission lines for enhancing the transmission capbility, thus improving the overall efficiency.
DIFFERENT COMBINATIONS OF HTLS CONDUCTORS
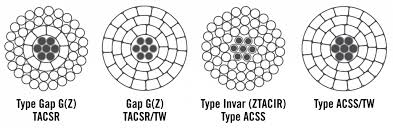
Steel/ coated steel/ steel alloy core with an envelope of thermal-resistant aluminum alloys
ZTACSR
- Common constructional feature like ACSR conductors.
- Core is formed of galvanized steel wires with envelope of TAL (thermal resistant aluminum alloy) or ZTAL (thermal resistant aluminum alloy with zincronium added) strands.
- Conductivity and tensile strength of TAL and ZTAL conductors are similar to electrical grade aluminum conductors.
- Elevated temperature withstanding capacity in the range of 150-200 degrees celsius without degradation in mechanical strength.
- Thermal elongation similar to ACSR, and hence the conductor exibits no low sag properties.
- Suitable for uprating normal ASCR lines with similar electrical clearances because of enhanced thermal endurance which aids in more current carrying capacity.
ZTACIR / STACIR (Conductor with INVAR core)
- Common constructional feature like ACSR conductors.
- Core is made up of strands of aluminum-clad invar alloy steel with an envelope of ZTAL strands.
- Low coefficient of thermal expansion of the core enhances thermal-sag properties of these htls conductor.
- Conductivity is slightly less than conventional ACSR conductors.
- Tensile strength is less.
- Elevated temperature withstanding capabilities with a maximum continous operating temperature of 210 degree celsius.
- Current carrying capacity is 2 times that of a conventional ACSR conductor.
- Prestressing required for lowering knee point temperature.
- Cladding can improve conductivity if needed.
GZTACSR or GAP CONDUCTOR
- There is a gap between the envelope and core which permits the independent movement.
- The radial gap is filled with heat resistant grease to reduce friction, water penetration and corrosion.
- Core is made of galvanised steel with ZTAL conductors forming the envelope.
- Envelope is of trapezoidal shape for compact stranding, increased cross-sectional area, and lowering resistance.
- Similar electrical properties as a TACSR conductor.
- It is a low sag conductor and thus can be operated at elevated temperatures than conventional ACSR.
- Sag of the conductor is dependent on sag of the core because the knee point temperature is at errection temperature, thus allowing low sag at very high temperatures.
- The grease used must have a drop point of atleast 300 degree celsius.
- The oil separation point of the grease should be optimal for preventing grease to flow to the outer surface.
- The grease must retain its properties over varied environmental conditions.
- Complex installation with increased labour.
- Best suited for snowy areas because trapezoidal envelope accrues less snow.
Steel/ coated steel/ steel alloy core with an envelope of annealed aluminum
ACSS and ACSS/TW
ACSS aluminum conductor steel supported
- Core can be made of steel (high strength/extra high strength / ulta high strength / michmetal / alloy clad steel) with envelope of fully annealed aluminum strands.
- Appearance of these htls conductor is same as ACSR conductors.
- Trapezoidal and round shape strand configuration available with equal dia and area.
- Enhanced current carrying capability because of annealed aluminum envelope.
- Lower tensile strength of envelope is mitigated by high strength steel core.
- Less thermal elongation of steel results in better low sag properties.
- Low tension in aluminum envelope helps in no creep under day to day tension.
- Galvanisation of steel core cannot handle temperature above 200 degree celsius.
- Mischmetal coating on the steel can withstand 250 degree celsius of constant operation without degradation.
- Mischmetal and alloy clad cores are more robust. However, mischmetal has superior corrossion resistance.
- The knee point temperatures are relatively low because of low tension envelope.
- Prestressing helps reduce the damage due to vibration fatigue during challenging installation like river crossing also aiding into reduce the knee point further.
- High temperature adaptable clamps to be used for allowing maximum temperature.
- Installation of these htls conductor is similar to ACSR, however softer annealed aluminum strands are to be handled with care.
- No dragging in ground, over rocks etc.
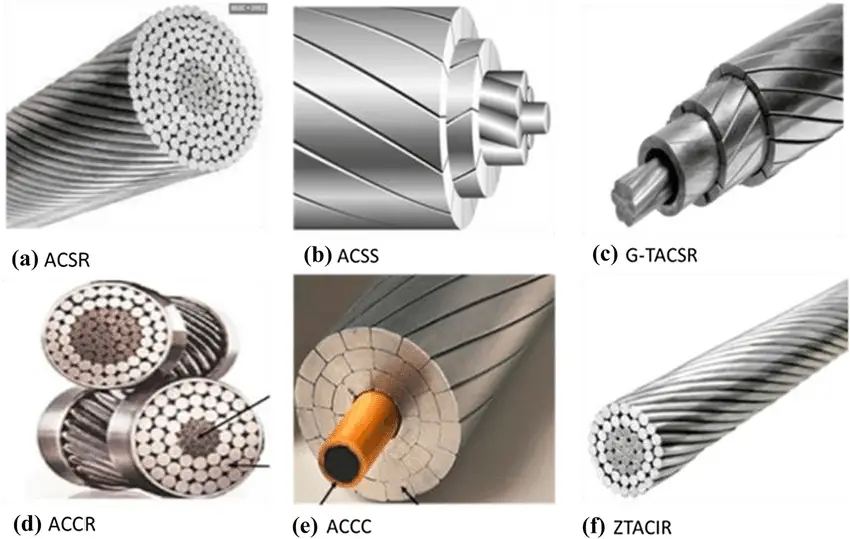
Metal-matrix composite (MMC) core with an envelope of thermal-resistant aluminum alloys
ACCR
- Core is made from metal matrix composite MMC and envelope with thermal resistant alloy.
- MMC includes wires of alumina fibers in a matrix formation, with strength 8 times of aluminum and stiff like steel.
- Core has low coefficient of thermal expansion in comparision to steel above the knee point.
- Core is lighter than steel and therefore less weight.
- Composite core is better in strength, conductivity and modulus of elasticity than steel.
- Can be operational with maximum temperature of 210 degree and 240 degrees at emergencies with AT3 alloy envelope.
- No issues of corrossion and magnetization as it is all alluminum conductor.
- Compression type hardware for dead end joints are split into two parts one holds composite core, outer sleeves provides the grip to envelope.
- Since the composite core are of anisotropic material, having high tensile strength but they are bad in handling bending force. Thus these htls conductors are fored to a high bend radius to avoid damage.
- While installation, correct size of diameter sheaves, bull wheel size, pulling tension matters to prevent any low bending.
Polymer-matrix composite (PMC) core with an envelope of annealed aluminum/ thermal-resistant aluminum alloy (Carbon Composite Core (CCC) Conductor)
ACCC, CFCC, HVCRC, ACFR
- Core is made of polymer matrix composite PMC like carbon fiber in resin or epoxy resin matrix or with thermal resistant alloy envelope.
- Corrossion free core as protected by annular sleeves
- Envelope can be round, trapezoidal of Z-shapped.
- PMC core has higher tensile strength which compensates the low strength envelope.
- Envelope is fully annealed for better conductivity.
- Core has low coefficient of thermal expansion which helps exibits low sag properties of the conductor at elevated temperature.
- Low sag and less weight helps increase the tower spans.
- Since the core is smooth and carries bears maximum tensile force, therefore the dead end assemblies must have strong crimps and aluminum press for better grip arround the core.
- Core is corrossion resistant along with resistance from vibration, UV radiation,corona and cyclic load fatigue.
- Composite carbon core has the lowest thermal sag, but due to the elastic core, it sags more under ice loading.
- Extra high strength composite core can be used for regions with heavy ice loads for enhanced sag values.
- Special fittings and hardwares are essential for these htls conductors as they are highly anisotropic.
CURRENT CARRIYING CAPACITY OF HTLS CONDUCTORS AT VARIOUS TEMPERATURES
S. No. | HTLS Conductors | Dia (mm) | Resistance at 20°C (Ohm/km) | Operating Temperature (°C) | Ampacity (A) |
1 | Al59 | 31.77 | 0.0497 | 75 | 656 |
85 | 841 | ||||
95 | 987 | ||||
2 | TACSR | 31.77 | 0.0556 | 75 | 620 |
85 | 794 | ||||
95 | 931 | ||||
125 | 1237 | ||||
150 | 1430 | ||||
3 | ACCC | 31.77 | 0.0418 | 75 | 710 |
85 | 910 | ||||
95 | 1068 | ||||
125 | 1421 | ||||
150 | 1644 | ||||
180 | 1866 | ||||
4 | STACIR | 28.95 | 0.0599 | 75 | 585 |
85 | 744 | ||||
95 | 869 | ||||
125 | 1149 | ||||
150 | 1324 | ||||
180 | 1499 | ||||
200 | 1601 | ||||
210 | 1649 | ||||
5 | GZTACSR (Gap) | 29.9 | 0.05134 | 75 | 629 |
85 | 801 | ||||
95 | 937 | ||||
125 | 1242 | ||||
150 | 1433 | ||||
180 | 1623 | ||||
200 | 1735 | ||||
210 | 1787 | ||||
6 | ACSS | 31.77 | 0.0521 | 75 | 633 |
85 | 810 | ||||
95 | 950 | ||||
125 | 1261 | ||||
150 | 1457 | ||||
180 | 1652 | ||||
200 | 1766 | ||||
210 | 1820 | ||||
250 | 2018 |
This article is a part of the Cables and Conductors, where other articles related to the topic are discussed in details.