Cable laying is a very essential part of any electrical installation. It helps optimize the power flow, reduces electromagnetic interferences on control cables, reduces fire risks, etc.
Table of Contents
MINIMUM PERMISSIBLE BENDING RADII OF CABLE LAYING.
The electrical power cables should not be bent in a very sharp radius in the process of cable laying because anisotropic insulation are very prone to failure on application of bending stress. Also the voltage distribution does not remains uniform in sharp bends, which results in high electric field concentration, developing more voltage stress and can cause insulation failure. Therefore, minimum bending radius for cable laying as per IS-1255 becomes very essential to follow. It is to be noted that D is the outer diameter of the cable.
Power Cables Up to 1.1KV
- The minimum bending radius for PILC cable laying with a single core is 20D and the multi-core is 15D.
- Similarly, the minimum bending radius for PVC and XLPE cable laying with a single core is 15D and for multicore cable it is 12D.
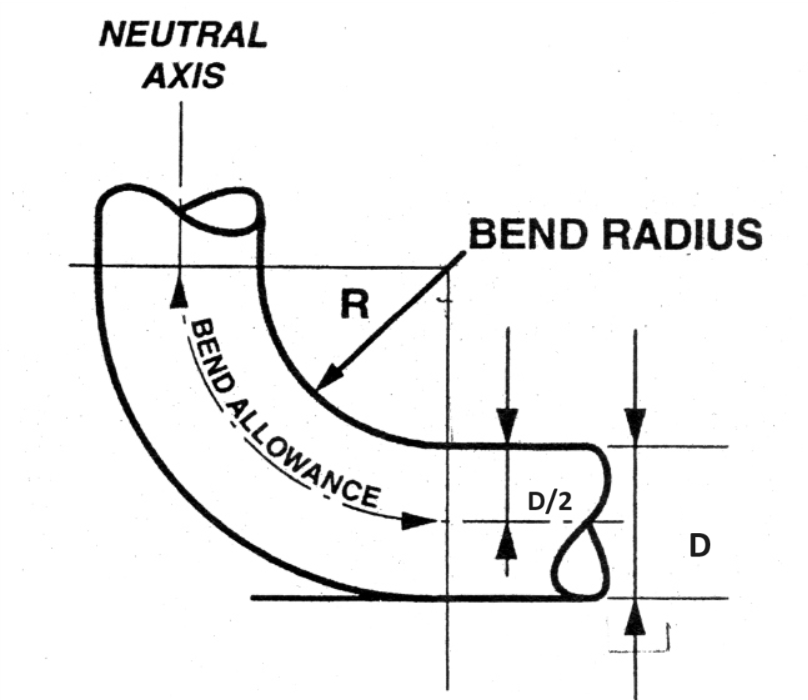
Power Cables above 1.1 KV to 11KV
- The minimum bending radius for PILC cable laying with a single core is 20D and multi core is 15D.
- The minimum bending radius for PVC and XLPE cable laying with the single core is 15D and for multi-core cable, it is 15D.
Power cables above 11KV
- The minimum bending radius for PILC cable laying with a single core is 25D and multi core is 20D.
- The minimum bending radius for PVC and XLPE cable laying with the single core is 20D and for multi-core cable it is 15D.
- At joints and termination of cables, in cable laying, the bending radius should be above 12 times the diameter of the insulation.
MAXIMUM PERMISSIBLE TENSILE STRENGTH (PULLING) OF POWER CABLES
While pulling a cable during cable laying, it should be kept in mind that the maximum pulling force should not be over the advised limits. Otherwise, the cable may undergo internal damage which can affect the conductivity along with insulation failure,
Let, ‘D’ be the diameter of the cable in millimeters, then the maximum permissible pulling force, P in newtons are:
- For PVC and XLPE insulated armoured cable, P = 9D2
- For PVC and XLPE insulated un-armoured cable, P= 5D2
- Paper insulated armoured power cable belted and H type, P = 3D2
- HSL cables, P = D2
When the cable’s conductor are directly pulled by a pulling eye, the maximum tensile strength depends on the cross-section and material of conductor,
- Aluminum conductors: 30 N/mm2
- Copper conductors: 50 N/mm2
Expected percentage pulling force when cables are pulled by a winch
- In trenches with large bends: 15-20%
- In trenches with 1-2 bends with 90 degrees each: 20-40%
- In trenches with 3 bends of 90 degrees each assuming supports at corners: 50-60%
- In trenches for bends totalling 360 degrees: 100%
Belt type power cables:
In these types of cables, the conductors are bunched together, impregnated paper insulated, and bonded by a paper belt. Fibrous dielectric materials like jute are used to fill the gap between the insulation and the belt and then armoured with a metallic screen.
H-type power cable:
These have three paper-insulated cores covered by perforated metallic screens which are grouped together by a metallic tape surrounded by a lead sheath. Both the sheath and metallic screen are grounded.
S-L type power cable:
These are similar to H-type cables with lead sheaths for individual cores. The advantage is that core-to-core breakdown is minimized in this type of construction. However if subjected to moisture, the dielectric strength may suffer badly as the individual seaths are leanner.
DEPTH OF POWER CABLES LAYING:
The minimum depth for cable laying from the ground surface to the top of the cable should be practiced as below:
- For cables of 3.3 KV to 11 kV: 0.9m
- Cables of 22 kV, 33 KV: 1.05 m
- Low voltage and control cables: 0.75 m
- Cables at road crossings: 1.00 m
CLEARANCES IN CABLE LAYING:
The desired minimum clearances are as follows.
Power cable to power cable – Clearance is not necessary. However, the larger the clearance, the better would be current carrying capacity. This is because heat can be transferred by conduction, convection, and radiation. And heating of cables lowers its current carrying capabilities.
- Power cable to control cables: 0.2m
- Power cable to communication cable: 0.3m
- Power cable to gas/ water main: 0.3m.
CABLES LAYING ACROSS SERVICE ROADS:
- For the cables crossing road, hume pipe or grade B GI pipes can be used as a duct under the road for crossing. Additional pipes must be laid for future provisions.
- The joints between two pipes must be covered with collars for non accumulation of dust and pebble in the joints.
- The inner diameter of the pipe must be atleast 1.5 times the outer diameter of the cable.
- The pipes shall withstand heavy load and hence shall have high mechanical strength.
- Padding should be present at entry and exit of the pipe.
- Bending radius if needed shall be atleast of 1.5 meters.
- No single core cable shall be laid in one pipe. Instead a trefoil formation of three phase of same system shall be practiced in single pipe.
CABLE LAYING ON RACKS
- Spacing for cables in the racks has to be sufficient as they are fixed to the walls with fabricated support for easy installation and replacement.
- The clearance between two racks vertically must be 0.3 meters and the spacing between the cable and the wall must be atleast 25mm. The width of the rack or tray shouldn’t exceed 0.75 meters.
- With or without spacers each tray shall have only one layer of cables. Cable stacking on two three layers per tray or rack can result in decrease of current carrying capacity of the conductors greatly.
- Galvanized trays shall be used and if not, the trays must be painted with anti corrossive paint with good finishing.
- Single core cables can be clamped at suitable intervals on horizontal trays, however there is no need for clamping multicore cables. Vertical clamping shall be done with a distance less than 2 meters.
Cable laying with the help of J-hooks mounted on the walls or held by catenary wires is also practiced.
Cable laying in unventilated tunnels, reduces the current carrying capacity of the cable as the heat developed in the cable cannot escape the tunnel. The heating of cables inside tunnel is a function on the power loss from the cable and can be calculated by:
T=W/3P, where T is the rise in temperature above the ambient in degrees Celsius, W is the power lost per meter length of the cable and P is the perimeter of the tunnel.
It must be noted that only the surfaces that dispose of the heat should be taken in the perimeter calculation.
This article is a part of the Cables and Conductors, where other articles related to the topic are discussed in details.